| HARVI I | HARVI I TE
| HARVI II
| HARVI II TE
| HARVI II LONG
| HARVI III
| HARVI III AERO
| HARVI IV
|
---|
| 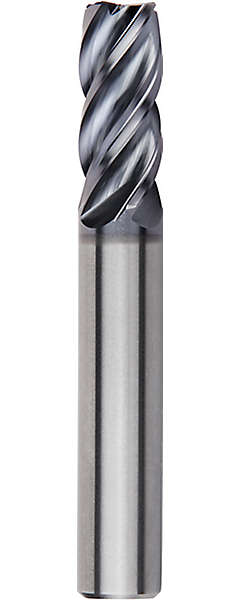
| 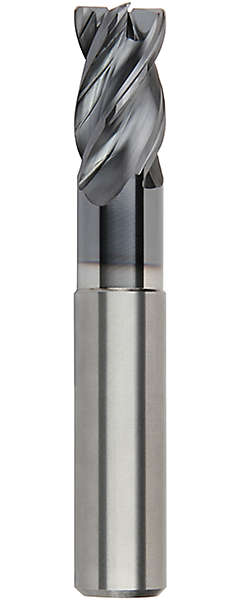 | 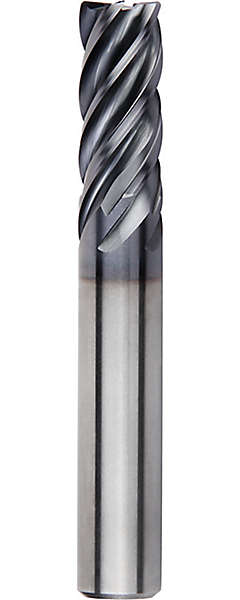 | 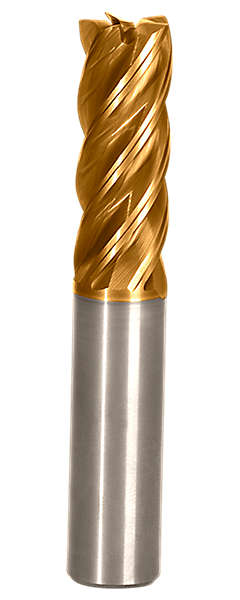 | 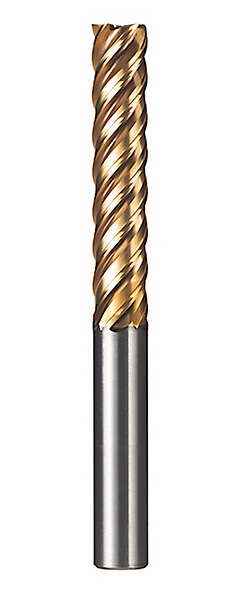 | 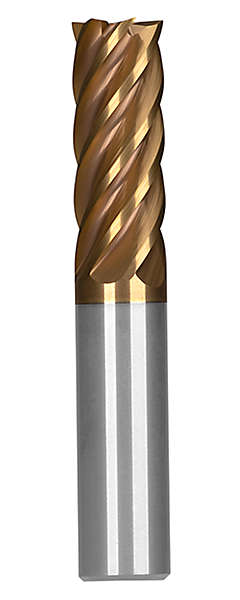 | 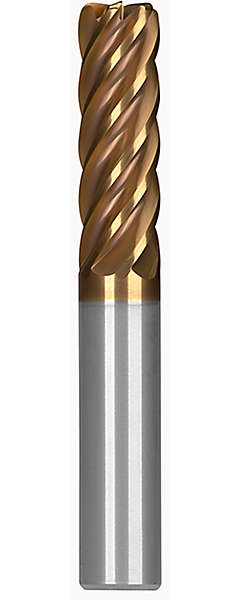 | 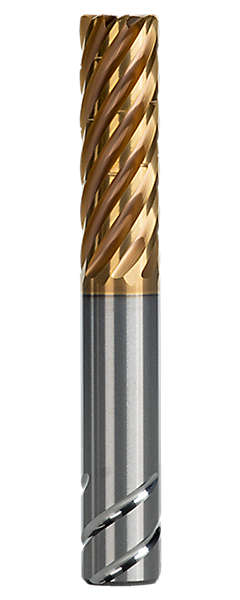 |
---|
Flute | 4 | 4 | 5 | 5 | 5 | 6 | 6 | 8 |
---|
Materials | Steels Stainless Steels Cast Iron High Temp Alloys and other HRSA Hardened materials up to 48HRC | Steels Stainless Steels Cast Iron High Temp Alloys Hardened materials up to 48HRC | Steels Stainless Steels Cast Iron High Temp Alloys Hardened materials up to 55HRC | Steels Stainless Steels Cast Iron High Temp Alloys Hardened materials up to 55HRC | Steels Stainless Steels Cast Iron High Temp Alloys Hardened materials up to 48HRC | Steels Stainless Steels High Temp Alloys Hardened materials up to 55HRC | Steels Stainless Steels High Temp Alloys Hardened materials up to 55HRC | Steels Stainless Steels High Temp Alloys Hardened materials up to 55HRC |
---|
Applications | Slotting Side & Shoulder Milling Plunging High Efficiency Milling Trochoidal Milling Ramping 3D Profiling | Slotting up to 2xD Side & Shoulder Milling Plunging High Efficiency Milling Trochoidal Milling 3D Profiling High angle ramping up to 45º | Slotting Side & Shoulder Milling High Efficiency Milling Trochoidal Milling Ramping up to 3° | Slotting up to 2xD Side & Shoulder Milling High angle ramping up to 45° High Efficiency Milling Trochoidal Milling Plunging | Side & Shoulder Milling High Efficiency Milling Trochoidal Milling | High Efficiency Milling Dynamic Milling Side & Shoulder Milling Ramping Trochoidal Milling 3D Profiling | High Efficiency Milling Dynamic Milling Side & Shoulder Milling Ramping Trochoidal Milling 3D Profiling | High Efficiency Milling Dynamic Milling Side Milling Peel Milling Ramping up to 2° |
---|
Diameter Range | 1/8 - 1” (4-25mm) | 1/16 – 1.25” (2-25mm) | 1/4 - 1” (4-25mm) | 1/8 - 1.25" (4-25mm) | 1/4-1” (6-25mm) | 3/8–1.25” (10-25mm) 1/8–1.25" incl. Taper BN (4-25mm incl. Taper BN) | 1/4–1.5” | 3/8-1" (10-25mm) |
---|
Best For | General versatility and reliability is required for roughing and finishing of multiple materials | Maximum versatility and process security is required, but there is a low chance of dynamic milling and high chance for heaviest and most aggressive cuts | General versatility for roughing and finishing of multiple materials with higher metal removal rates | Maximum versatility is required with a high chance of dynamic milling. Better choice for narrow trochoidal slots for better chip management. | Long reach applications, best choice for finishing and fine finishing operations | When dynamic milling & high efficiency milling with high productivity. Better choice for wider trochoidal slots. | Same as HARVI III, but ideal for Titanium | When only dynamic milling and high efficiency milling with highest productivity, best choice for pocketing applications |
---|